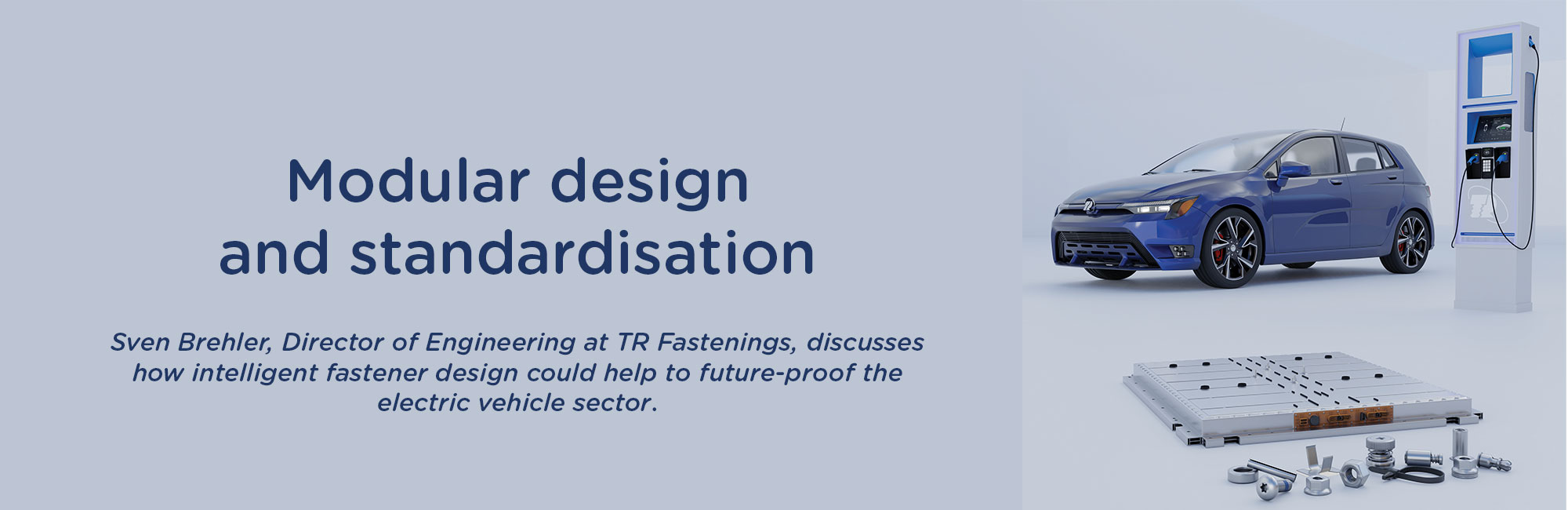
Share this article
Sven Brehler, Director of Engineering at TR Fastenings, discusses how intelligent fastener design could help to future-proof the electric vehicle sector.
As innovation within the electric vehicle (EV) market continues to gather pace, many manufacturers are looking at how modularity can improve the design, performance and overall lifecycle of current and future vehicles. Naturally, this move towards more modular designs is placing new demands on fastener manufacturers to develop products capable of meeting the requirements of more integrated components.
With 34 locations in 18 countries, TR Fastenings is involved at the forefront of fastener design and supply to the global automotive sector, in particular with the Tier 1’s. The rise of the EV market has presented new opportunities – and challenges – for the fastener provider. The companies engineering, research and development capabilities enable it to work closely with its customers to develop products that are not only optimised in terms of design and performance, but also in regard to their recyclability, assembly efficiency, and overall lifecycle.
Now EV manufacturers are looking at modular design as a completely new concept. This is a great opportunity for us, as the initial design and concept of the application is where we can ensure fasteners become an integral part of the whole design early on. This specifically works well when looking at light-weighting, for example.
Working with its customers from the beginning of the design process allows TR to not only optimise the design of the fasteners required for a specific part, but it also improves the overall sustainability of the vehicle.
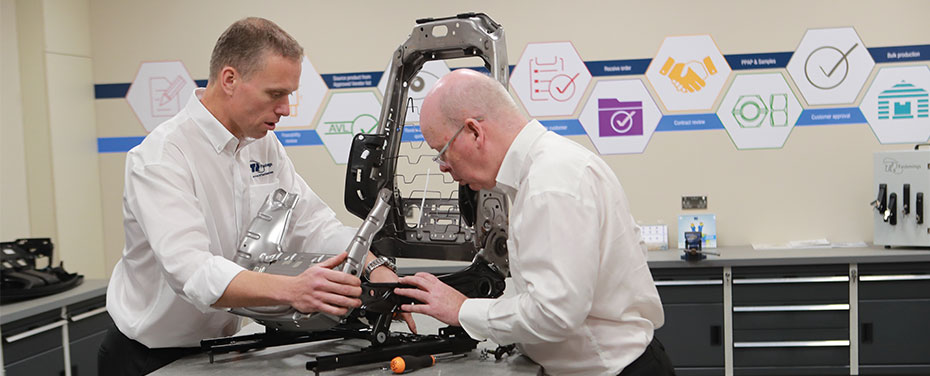
“For example, let’s assume that a vehicle has an average lifespan of 12 years, after which it will need to be taken apart so that its components can be recycled and reused,” Brehler explains. “Anything that we do not get right up front, we will pay for later on. It’s becoming much more important to also look at the reusability and recyclability of the products used in EVs at the early design stage.”
Whereas in the past automotive manufacturers have leaned towards gluing or welding parts together to create permanent fixings, the increasing importance placed on improving the lifecycle of new vehicles means it is important that these units can eventually be taken apart. We are already seeing assembly methods changing in other industry sectors with the new legislation in Europe, ‘The Right to Repair’.
“The move towards modular design is where it gets interesting” Brehler adds. “With every new development, it opens the door for us to look at reapplying or developing new products and bespoke items that will ultimately improve the recyclability and sustainability of future vehicles. Embracing modular design can help to elongate the life of not only the parts themselves, but also of the entire vehicle as it allows various components to be replaced, which has often not been possible previously.”
Although known widely for supplying threaded fasteners, TR Fastenings also supplies bespoke product such as Compression Limiters and Plastic Components, increasingly used in assemblies e.g. battery housings. Such items are designed in line with new technical challenges posed by the rapid acceleration of EVs and battery technology, requiring capabilities such as heat and Cable Management, conductivity and electrostatic finishes.
“With light-weighting, we are seeing more aluminium and high tensile steels being used, which pushes the boundaries of current products,” Brehler explains. “We are also seeing requirements for silver-plated and tin-plated parts for connectivity, as well as special plastic parts that work as a barrier or in closing the battery packs or Cable Management. The EV market is providing many more opportunities to develop new products with our customers.”
Of course, the rapid advancement of EV technology is not without its challenges, Brehler admits. In particular, the sector is currently lacking standardisation. He gives EV charging plugs and units as an example, the compatibility of which often varies between the vehicles of different manufacturers. With no globally agreed standard, people have little choice but to replace their charging units when they purchase a new vehicle, which is both costly and creates unnecessary waste.
This is also seen on the battery side, Brehler observes. As there is no standardisation for the chemistries used within batteries, they must be separated individually in order to be disposed of or recycled.
“It is not only the development of new products, but also the application of new products which is becoming very important,” he says. “Being able to integrate an existing fastener that has already been tested and proven into a customer’s application is just as important as developing your own product. So, if you can find a new application for a fastener that has already been tried and tested, you have already covered that part of the process.”
This is something that TR Fastenings is keenly focused on: “This is actually driving the technology forward and helping to further develop the existing products we have.”
An example of this is the company’s EPW Self-Extruding Screw, which Brehler says was developed initially for the white goods sector. The TR team have developed this even further as this product has potential to be used for the EV market.
“We have seen a lot of innovation, ideas and technology from the electronics and telecoms industries moving into the existing automotive market, and that is why we are seeing so many changes in design and development,” he says. “We are able to take our experience and expertise from other industries and apply it to the EV sector.”
This transfer of knowledge and innovation has also been seen in the Formula One market: “Formula One is moving towards the electric vehicle and they are pushing the industry forwards massively,” Brehler observes. “We can see them adopt some of the technologies we are looking at, especially light- weighting, through looking at different types of screws that push the boundaries and drive weight down. Taking things apart is also extremely important in Formula One, so we can see those benefits already carrying through from different industries into the mainstream EV market.”
Returning to the need for improved modularity and standardisation in the EV market, Brehler believes the two concepts go hand-in-hand.
“The lifespan of EVs is going to increase due to less moving parts and other factors such as autonomous driving leading to less wear and tear, which means there will be a greater focus on the coatings on fasteners within these vehicles,” he explains. “Corrosion will be one of the major feats we have to overcome, because you can’t take a corroded fastener out of a vehicle, which will impact the recyclability process. How will we take apart a vehicle in 30 years’ time? That’s what everyone is talking about now, and that is what will prompt global standardisation within the industry going forwards.”